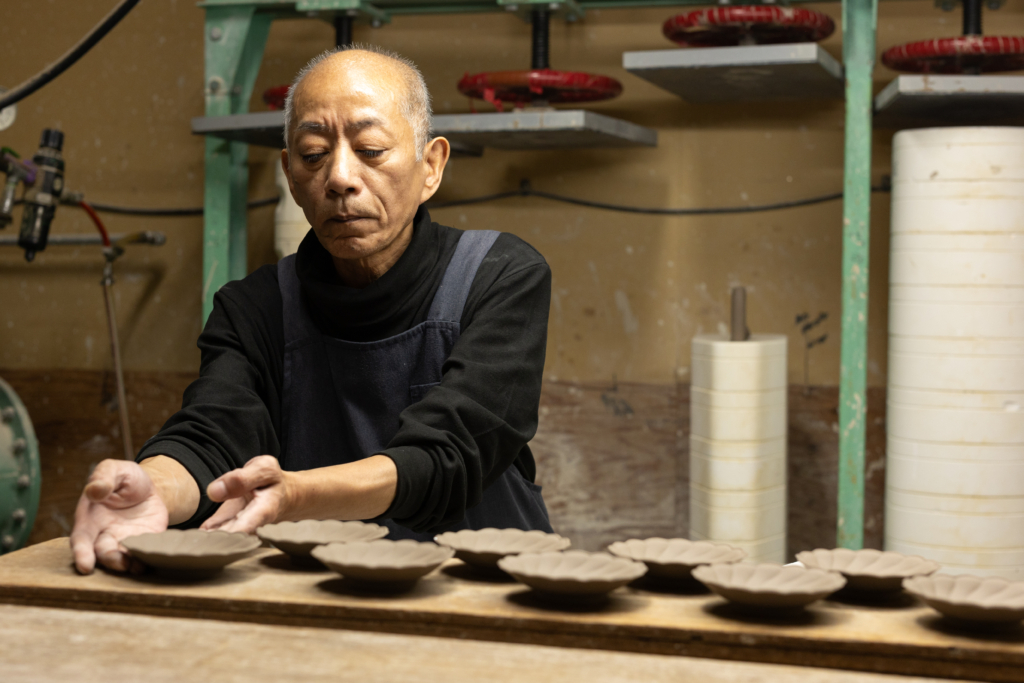
Infusing Japanese Spirit into Shiro Kutani “tocowa”
Miyayoshi Seito, founded in 1972 and located in Komatsu City, Ishikawa Prefecture, is a kiln specializing in molding the raw materials for Kutani ware. The person in charge of guiding visitors and tour experiences at the kiln is Chen Miyayoshi Wei, the second-generation son-in-law. In the world of Kutani ware, which has been shrinking in scale, he has played a key role in developing the company’s own brand, “tocowa,” leveraging the strengths of their raw material molding business. What does Chen Miyayoshi Wei consider to be his “role” as a Kutani ware kiln owner? And what is the “spirit” underlying his work?
What Can Be Done as a Kutani Ware Kiln?
Miyayoshi Ceramics, based in Komatsu City, Ishikawa Prefecture, has been molding raw materials for Kutani ware since 1972. The business is currently led by the second-generation owner, Katsushige Miyayoshi, and supported by his son, the third-generation heir, and his son-in-law, Chen Miyayoshi Wei. Originally from Taiwan, Mr. Chen-Miyayoshi has settled in Komatsu City and is dedicated to conveying not only the excellence of Kutani ware but also the spirit of craftsmanship embedded in the works.
Miyayoshi Seito operates as a family business with more than 20 employees. The kiln holds a 70% share of the raw material shaping market in the Kutani ware region and is an indispensable part of the local Kutani ware community, supporting not only the color painting wholesalers in Komatsu but also Kutani ware artists across the country.
The raw material molding process at the workshop uses both machines, such as roller machines and pressure casting, as well as traditional handcrafting tools like the potter’s wheel and mold casting. For large orders of raw materials from major restaurants, machines are used, while more detailed requests from artists are handled by hand.
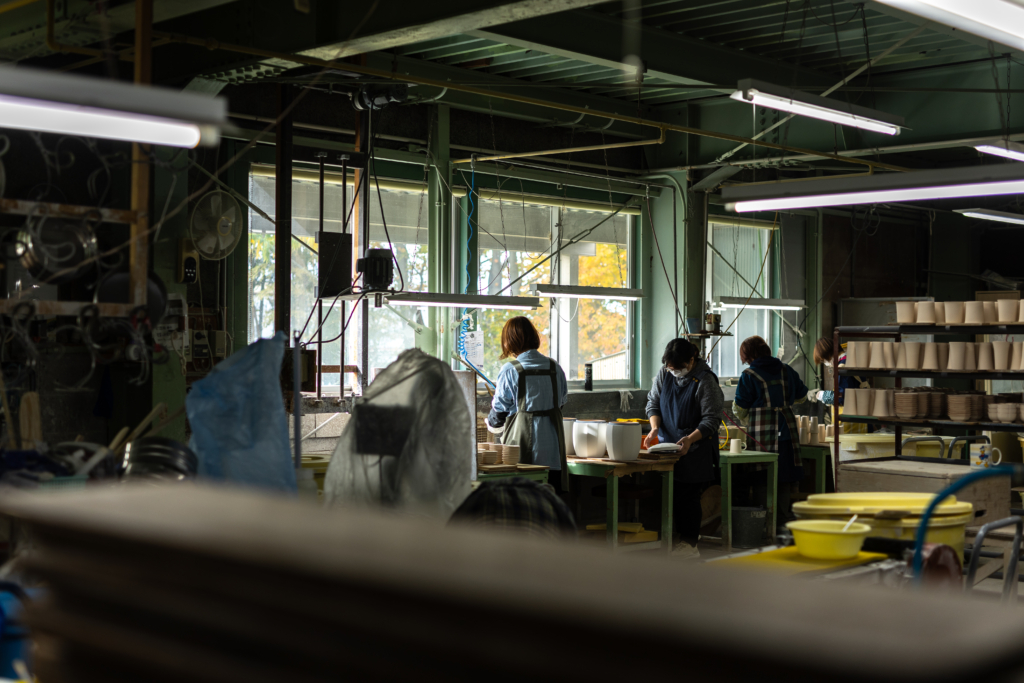
“The characteristic of the raw material for Kutani ware is its beautiful bluish-white color. This color is derived from the Hanasaka ceramic stone used as the raw material,”
Located just a few minutes away from Miyayoshi Seito is the Hanasaka Ceramic Stone Mountain, where the “Hanasaka Ceramic Stone” is mined and processed into the clay used for shaping the raw materials. Unlike the bright whiteness of Amakusa stone used in Arita ware, the bluish-white finish is due to the high iron content in Hanasaka ceramic stone. “You can’t call it Kutani ware without using Hanasaka Ceramic Stone,” as its unique bluish-white color captivates the hearts of many.
“However, the number of kilns specializing in raw material molding has been decreasing in recent years. In the past, there were said to be dozens of such kilns in Komatsu City, but with our type of mass production, now only ours and one other remain. If we were to stop, Kutani ware itself would no longer be sustainable. Every day, I feel the responsibility to continue creating as a kiln,”
Mr. Chen-Miyayoshi’s father-in-law, the president of the company, feels this responsibility even more strongly. “We must fulfill our role and contribute to the community,” he often says, emphasizing the importance of passing on Kutani ware to the next generation. Mr. Chen-Miyayoshi shared a story about his father-in-law’s unwavering commitment:
“When I first joined Miyayoshi Seito, there was a plan to establish a facility to promote Kutani ware as a tourist hub. The president, always thinking about what he could do for the community and Kutani ware, immediately agreed to the idea. At the time, he was the head of the kiln association and quickly went from kiln to kiln, personally asking for their cooperation in setting up the facility. However, it didn’t go smoothly.”
Due to the shrinking scale of the Kutani ware industry, many of the kilns, already in a somewhat negative position, were not interested in the new project. Naturally, very few kilns raised their hands in support. Despite this, the president did not give up. He kept visiting other kilns, bowing his head and asking for their help. His unwavering passion for the future of Kutani ware and his pride as a kiln master were evident.
“I could never do such a thing. It’s incredible,” says Mr. Chen-Miyayoshi. However, witnessing his father-in-law’s actions gave Mr. Chen-Miyayoshi the opportunity to reflect on his own role in the industry.
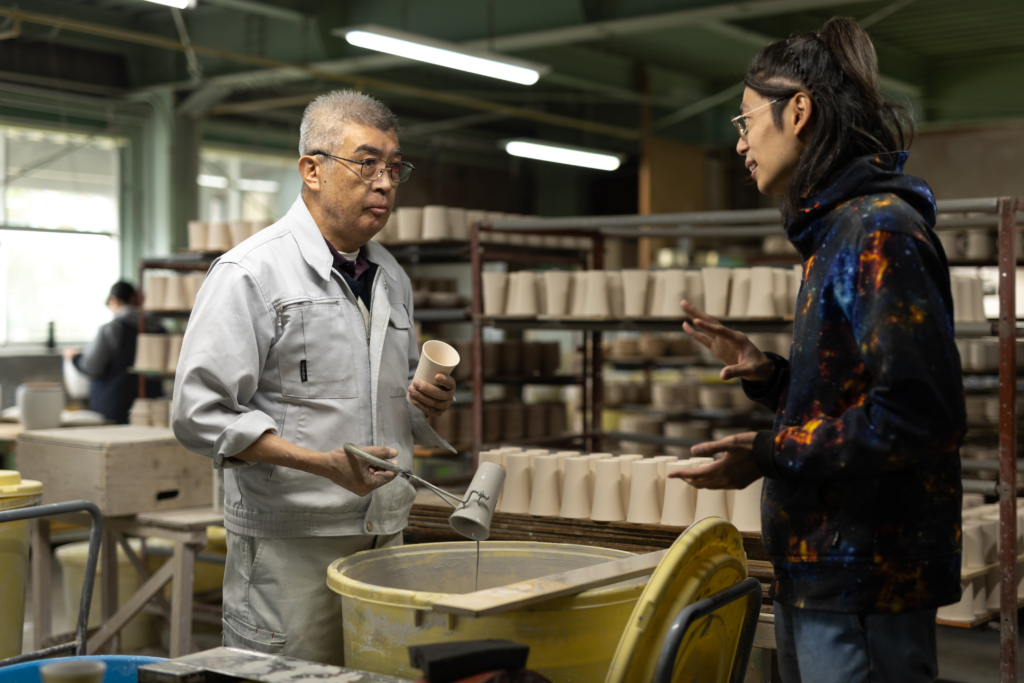
A New Challenge for the Kiln – White Kutani “tocowa”
In Kutani ware, there has long been a division of labor in the manufacturing process, with raw material molding, colored painting, and wholesalers each handling different stages of production and distribution. The pottery made by kilns specializing in raw material molding is passed on to wholesalers, who then distribute the painted products—either done in-house or by painters—to stores where customers can purchase them. Wholesalers, who control the sales channels, hold significant authority in determining the price of the products. In extreme cases, the price that the wholesaler pays to the kiln can increase tenfold or even more than a hundred times by the time it reaches the customer. On the other hand, kilns specializing in raw material molding rely on wholesalers to buy their products for their business to stay afloat. Sometimes, they have no choice but to accept the “price” set by the wholesaler, which used to be based on the wholesaler’s terms and is now known as the “wholesaler price.” This has been a long-standing custom. Mr. Chen-Miyayoshi experienced a similar situation when he first started working at Miyayoshi Seito.
“Honestly, I felt that this system no longer suited the times,” says Mr. Chen-Miyayoshi. “The value of the craftsman’s work, which is made with so much soul, should be properly communicated. Conveying the value of the work means, in turn, spreading awareness of the value of Kutani ware itself.”
At the same time, the situation with wholesalers was gradually changing. Many were closing due to a lack of successors, meaning that some kilns were losing their means of distribution. This prompted Mr. Chen-Miyayoshi, along with his wife and their third-generation brother, to embark on a new challenge: “To have the kiln directly deliver its work to customers.”
“In this case, since we don’t have strong design skills, we realized that if we tried to paint the pieces ourselves, we wouldn’t be able to create works that would be recognized by customers. So, we thought we should focus on our strength—raw material shaping—and offer ‘white’ pieces. We would sell them directly to the customers. That’s how our original brand ‘tocowa’ was born.”
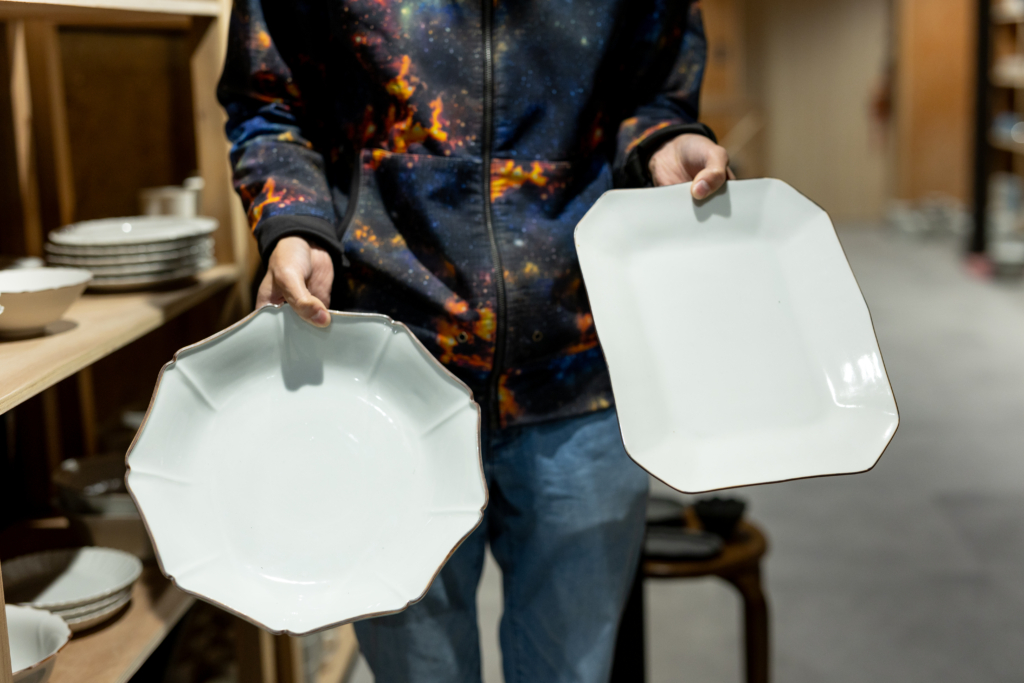
The works of “tocowa,” unified by a bluish-white color, present an entirely different impression from the colorful, vibrant Kutani ware often seen with its signature five colors and gold leaf. The natural hues of the Hanasaka ceramic stone used in the raw material shaping process are reflected in the pieces, which is something only a raw material shaping kiln can do. Despite their simplicity, the works of “tocowa” convey a dignified presence and have been well received by people of various age groups, earning the nickname “Shiro Kutani.(White Kutani)”
“Originally, there wasn’t a specific genre called ‘Shiro Kutani.’ It’s a name that naturally emerged among customers who loved the white ware over the past few years.”
The name “tocowa” is derived from the Shinto spirit of tokowaka, meaning “forever young” or “eternally vibrant.” It carries the resolve of Mr. Chen-Miyayoshi and the younger generation to correctly convey the value of the craftsman’s skills and the work itself directly to customers. It also reflects a deep, almost prayerful desire to honor the pride of the predecessors in the Kutani ware tradition.
However, due to the long history of Kutani ware, there may be some who view “Shiro Kutani” as an outsider within the tradition.
“Yes, that’s true. I’m sure some people think that way,” Mr. Chen-Miyayoshi says with a light smile.
“But as lifestyles change with the times, if white ware is what people desire, it is our role to create it. Moreover, the traditions and techniques we have inherited as a Kutani ware kiln over the centuries are all embedded in ‘tocowa.’ Ultimately, Kutani ware can only exist because of its white raw material. Even though our works may leave a different impression, they are still Kutani ware at their core.”
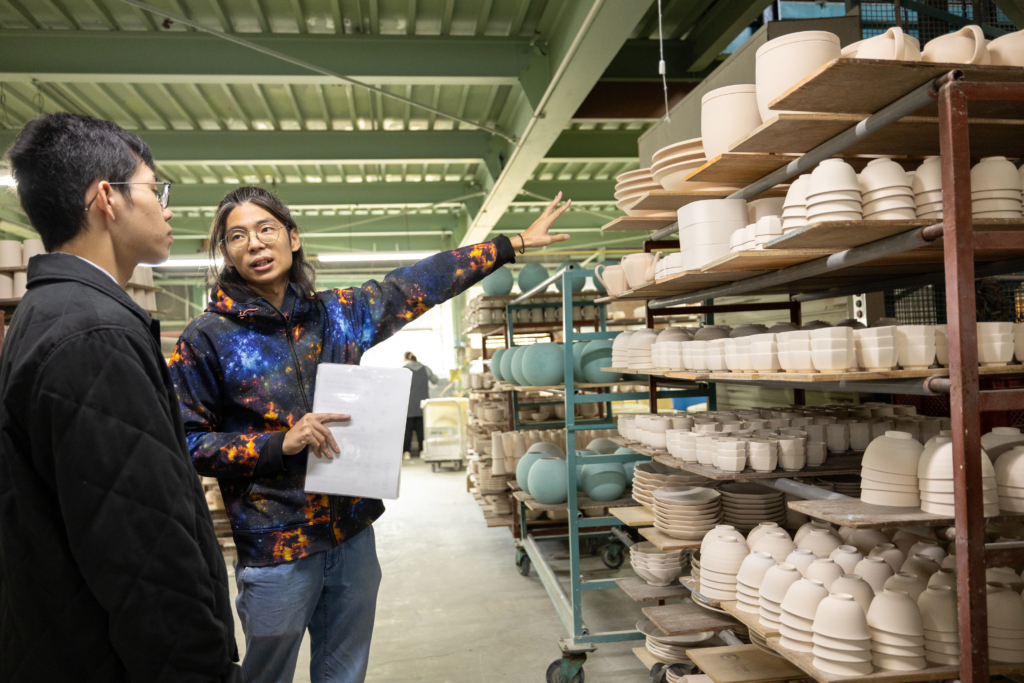
Why I Am Passionate About Kutani Ware
Born and raised in Taiwan, why does Mr. Chen-Miyayoshi have such a deep passion for Kutani ware? To understand this, it is necessary to look back at Mr. Chen’s own journey.
While studying Japanese at a university in Taiwan, Mr. Chen-Miyayoshi decided to study abroad to further immerse himself in the language. He entered a university in Chiba Prefecture, Japan, and went on to graduate school. After graduation, he chose to stay in Japan and became a staff member of a related organization affiliated with the university. For nearly ten years, he was involved in social education, moral education, and school education.
“Through my involvement in social education, I learned many things. I realized that, regardless of the environment or situation, it is important to think for oneself, find answers, and take action. I realized that I am the one who creates my own life. So, when I entered the world of Kutani ware and saw it shrinking, I began to think about how I should engage with it and what I should do,” Mr. Chen-Miyayoshi reflects.
His roots in understanding the value of Kutani ware and his role in its preservation seem to stem from the lessons he learned during his time in Japan.
Currently, Mr. Chen-Miyayoshi also serves as a guide for visitors to Miyayoshi Seito, where he leads tours of the workshop and offers hands-on experiences. One thing he always emphasizes during these tours is the dedication of the craftsmen.
“All the craftsmen work with love and prayers, facing their creations. I make sure to tell the visitors that they work with the hope that the customer will be happy. When customers hear this, they seem to develop a stronger attachment to the pieces they purchase and want to use them with care. But I always say, ‘Don’t be too careful, or our products won’t sell!’ and everyone laughs.”
Throughout the tours, Mr. Chen-Miyayoshi focuses on being the “Tsunagite” (the connector) between the customers and the craftsmen, trying to convey not only the beauty of the pieces but also the soul of the artisans who create them. Thanks to Mr. Chen’s guidance, the value of Miyayoshi Seito’s work becomes even deeper for the visitors.
The Spirit of Craftsmanship Embedded in Kutani Ware
Carrying on the company president’s belief that they must fulfill their role and contribute to the community; Mr. Chen-Miyayoshi expresses his desire to “continue promoting Kutani ware to a wider audience.” This is the purpose behind “tocowa.” Despite being seen as unconventional, he believes that being accepted by many as “Shiro Kutani” (White Kutani) is his role and mission.
“There is something else I learned when I worked in Chiba Prefecture. It’s ‘Japanese spirit.’ Through my exposure to various traditional Japanese cultures, I came to understand more about Japan as a country, and the Japanese people’s spirit of valuing others, things, and traditions. This ties directly into the ‘spirit of craftsmanship’ that is passed down through Kutani ware.”
Each piece of Kutani ware carries the prayer and soul of the artisan, as well as the wish of Mr. Chen-Miyayoshi and his team to share these creations with the world. All of this might be considered part of the “Japanese spirit.” Facing his role and the environment he was given with sincerity, sometimes relentlessly and courageously, Mr. Chen-Miyayoshi’s example teaches us the spirit that many Japanese may have forgotten.
Chen Miyayoshi Wei
Born in Taipei City, Taiwan. After studying Japanese at a university in Taiwan, he went on to study abroad at Reitaku University in Chiba Prefecture. After graduation, he became a staff member of public interest incorporated foundation affiliated with the university, where he was involved in social and school education. After marriage, he joined his wife’s family business, “Miyayoshi Seito,” and is currently involved in public relations, product development, and tourism.
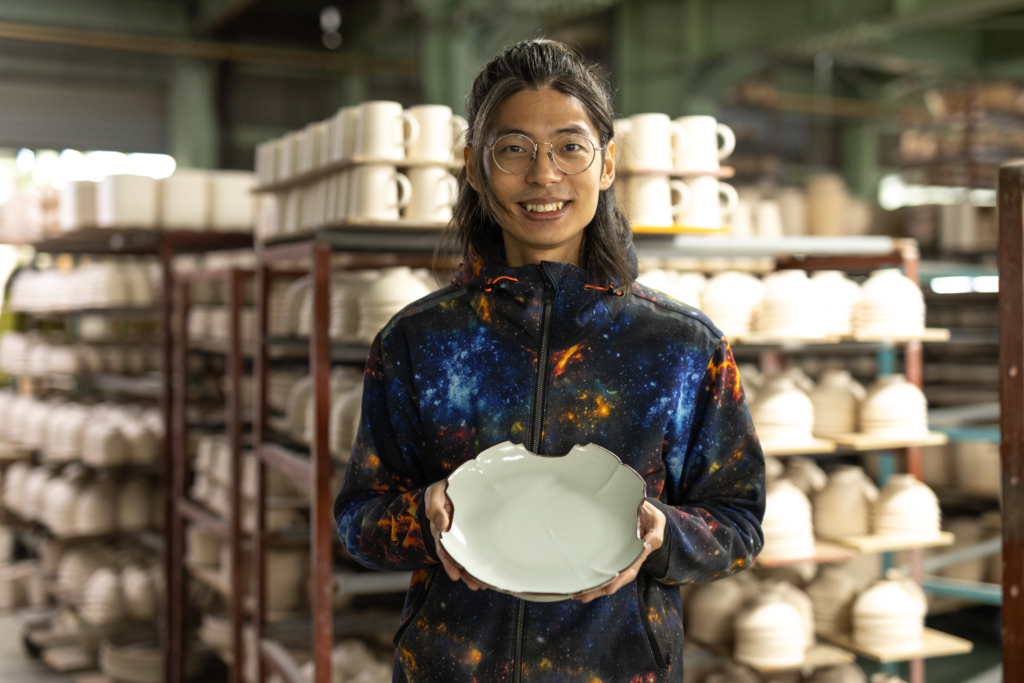
If you would like to visit Miyayoshi Seito and get further into the world of Kutaniyaki, please see the following information
Miyayoshi Pottery Workshop Tour Program
Highlights
・You can take a special guided tour of the studio with Mr. Chen.
・If you wish, you can experience the pottery making process.
・You can also try your hand at pottery making if you wish.
Information
Fee: From 4,000 yen per person
Participants: 1 to 6 people
Time required: about 1 hour
Included: Tour of Miyayoshi Pottery Studio
Meeting: Parking lot in front of Miyayoshi Pottery Studio
Language: Japanese (English interpretation service can be arranged upon request)
For reservation inquiries, please click here.